Future-Proofing Your Firm With Technology
SmartFocus on Traceable Construction Overview - SPRING 2019
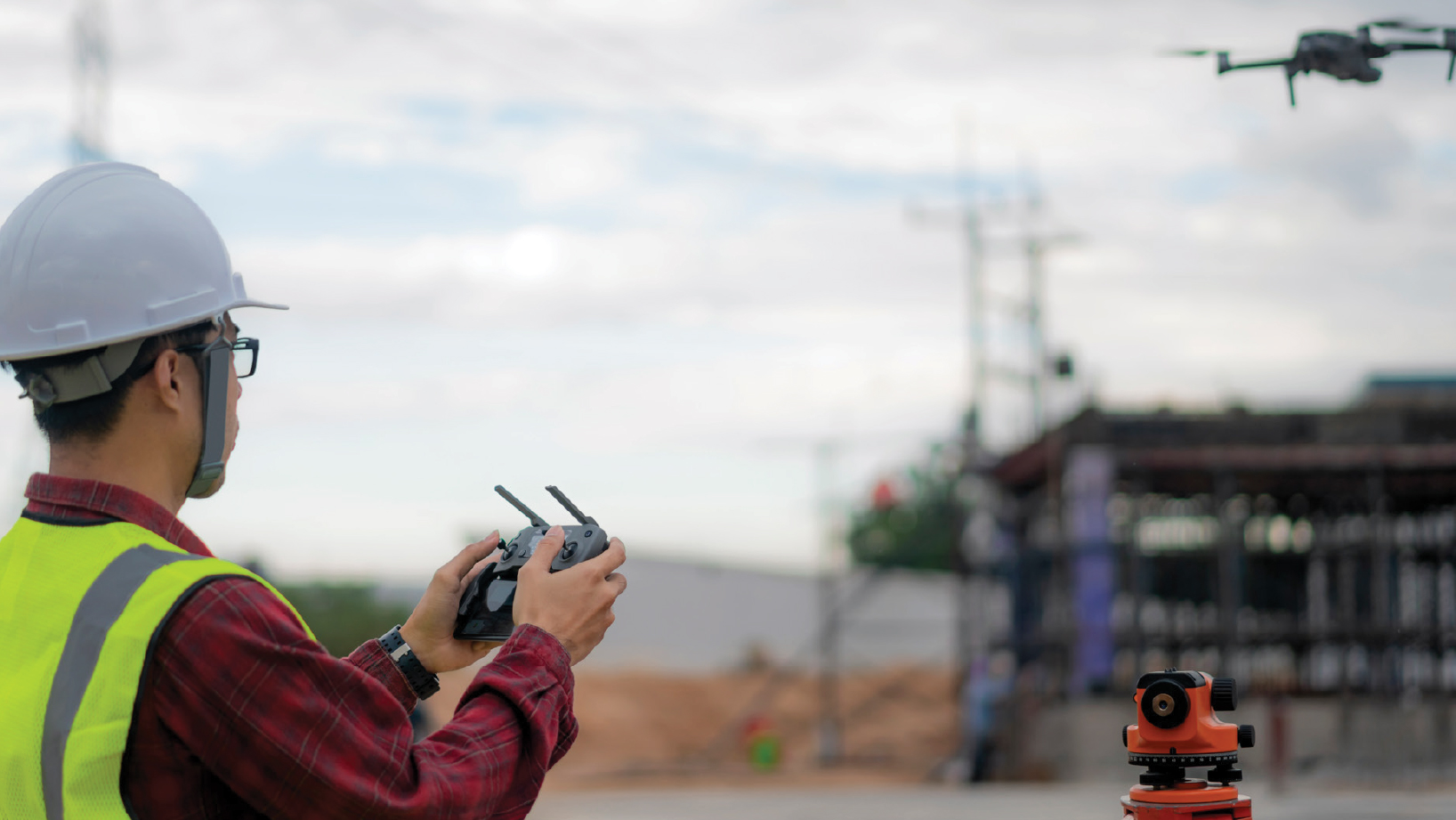
Technology is everywhere in the construction industry. Hardware and software are
used in every phase of a structure’s lifecycle. In fact, 54% of contractors reported using one advanced
technology, and 74% planned to add one or more by 2021, according to a survey by the U.S. Chamber of Commerce
and USG Corporation.
Difficulty integrating software and a preponderance of single-function specialty hardware can hinder
productivity, performance and precision.
That’s why it is important to look at these solutions as an ecosystem in order to identify bottlenecks
and roadblocks and seek out devices and systems that work together and have multiple capabilities.
“Many contractors are maximizing investment by purchasing hardware and software that can complete
multiple functions, which boosts ROI,” notes Brent Slawnikowski, senior account manager for Construction
BIM at FARO Technologies.
This approach future-proofs your enterprise by maximizing your workforce, increasing safety, improving
competitiveness and driving revenues.
Factors Driving Tech Adoption in Construction
The factors driving tech investment and adoption include:
- Growing Use of BIM.
Many clients now require the use of BIM and laser scans as deliverables to even bid on projects, which prompts more contractors to acquire laser technology for in-house use. This is cheaper than relying on outside contractors for the services, enables you to do fit-for-purpose scans, and improves collaboration and communication with others involved in the process. - Increasing Quality Standards.
“Old-school workflows and measures can’t be upheld anymore,” Slawnikowski says. “The standards we’re building to in AEC or manufacturing are much higher, and you can’t meet those without new technology that advances with these industries.” Whether you're manufacturing components or building pods for modular buildings, accuracy is crucial to keep costs in line and reduce risk. Advanced manufacturing processes enable faster production of mass-produced or custom pieces. That includes laser scanning and tracking technology, which ensures accuracy and quality assurance. A TechValidate survey of FARO users shows that 88% of respondents experienced reduced measurement and inspection time by 25% to 50% after implementing the solution. Construction has always been behind, but now it’s becoming a leader. This has to do with tech advancements. - Escalating Regulatory Verification Requirements.
As more federal and state regulations come online, keeping up with specific requirements for materials and geographies becomes more difficult. Many firms are turning to state-of-the-art cloud-based software systems that include regularly updated specs – such as F numbers or offsets. Because companies need to be in compliance with industry and local standards, they’re turning to technology that helps make that easier and more efficient. Reports generated from scan data and photography can also help establish compliance. - Continuing Need for Safety and Risk Reduction.
The Bureau of Labor Statistics shows that one-fifth of all workplace fatalities are in construction, and the leading cause is falls, followed by vehicle collisions and being struck by objects. Safety hazards can be reduced with technology that automates tasks or allows crew members to work from a safe distance. For example, drones enable contractors to “fly over” complex sites that are treacherous for humans to traverse. 3D laser scanners enable crews to get accurate measurements without climbing ladders, erecting scaffolding or using cranes. And because these technologies produce valuable visual data that lives online, this reduces the number of truck rolls back to the site, which further lowers risk. - Dwindling Workforce.
Technology helps contractors address the labor shortage in two ways. First, automation handles many rote and routine tasks, particularly in the administrative and project management arenas. Omitting that work frees up highly skilled workers to focus on more critical and higher-value activities. “When you have streamlined workflow and connectivity between pieces of technology,” Slawnikowski notes, “you get the most from the people you have and attract younger people to the business.” Second, advanced solutions like virtual reality, digital modeling and data analysis appeal to younger workers who might not consider construction and contracting as high-tech professions.
A Technology Ecosystem
All this hardware and software is amazing, but it has even more power to transform
your business when you
treat it like an ecosystem.
“Different instruments and software can actually create a challenge to getting work done when they don’t
work well together,” Slawnikowski says. “When you have to move between applications or devices, it slows
down the process and creates more opportunities for human error.”
Savvy firms purchase equipment and software that can multitask, which makes workflows more efficient and
reduces mistakes. One example: a 3D laser scanner, which is designed for surveying, can scan a deck for
floor flatness, determine location for MEP, and chart as-built conditions. Adding these capabilities
in-house allows a company to offer additional services to clients and do more work without having to add
more headcount or pay for specialty training.
It’s also crucial to make sure all the hardware and software support BIM with data gathering and
analysis.
The goal is an ecosystem of solutions that combine to generate a single source of truth, with details and
images of all activities in every stage of every phase — from bidding to hand-off to
decommissioning.
“You need one system to hold anything that’s captured in a moment in time so you can review
accountability
and responsibility, and to know who did the work or who were the contributing contractors,” Slawnikowski
says. “You want to use tech that can talk with different software platforms and hardware seamlessly.
Having
a system that’s streamlined that works together brings down overall costs, which saves you money and
brings
ROI faster.”
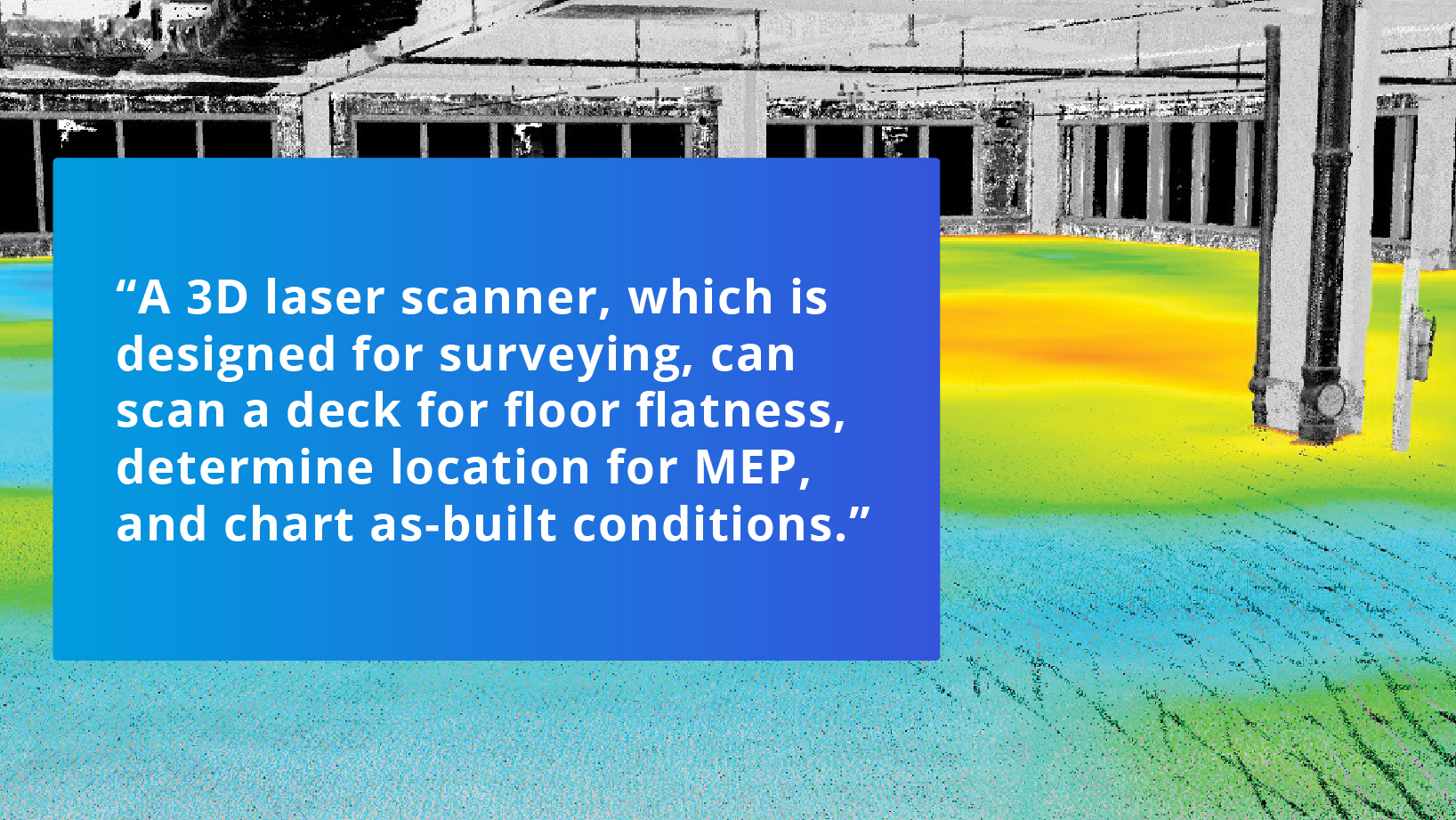
Now is the Time
Construction and related trades have been slow to adopt new technology, but with more
customers requiring
digitization and fewer people entering the field, embracing innovation is the best way to combat the
factors
that impede success.
The most competitive firms are already futureproofing their business against these rapidly approaching
labor
and industry challenges. Investing now in solutions that gather, track and deploy data will improve
overall
financial and operational performance and counteract the labor shortage.